Две другие оболочки выполняются из стеклопластика методом ручной выкладки. Одна из стеклопластиковых оболочек приклеена непосредственно к стальной трубе, а другая расположена по отношению к ней с некоторым зазором и образует аэродинамический контур носовой части. В зазоре между стеклопластиковыми оболочками расположены соединяющие их между собой узкие продольные элементы, выполненные также методом ручной выкладки из стеклопластика. Хвостовая часть лопасти выполнена практически полностью из композиционных материалов.
Одной из главных технологических проблем при производстве лопасти несущего винта вертолета Ми-26 оказалось образование складок в стеклопластиковых оболочках при изготовлении их методом ручной выкладки. Для лопастей несущего винта вертолета Ми-26 появление складок в стеклопластиковых оболочках не является фатальным, так как основные нагрузки (как уже было сказано ранее) несет стальная труба, являющаяся главным силовым элементом лонжерона. Однако трещины, которые могут появиться на месте складок слоев композиционного материала, – весьма неприятный эксплуатационный дефект. Несмотря на то, что значительная часть элементов лопасти несущего винта вертолета Ми-26 выполнена из композиционных материалов, она (с учетом перечисленных выше недостатков) уступает по эксплуатационным качествам лопастям, полностью выполненным из композиционных материалов.
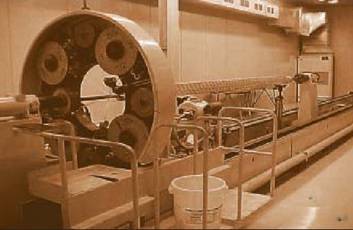
Фото 2
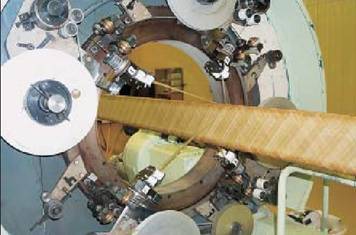
Фото 3
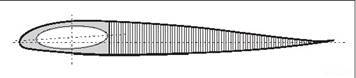
Рис. 4
Около 10 лет назад лопасть несущего винта вертолета Ми-26 была перепроектирована. Опытные образцы лонжерона лопасти были изготовлены методом намотки и успешно прошли усталостные испытания. Однако вследствие экономического кризиса работы по цельнопластиковой лопасти несущего винта вертолета Ми-26 были остановлены и технологическая оснастка законсервирована.
Для вертолета Ми-26 были разработаны, изготовлены и прошли полный цикл испытаний, включая летные, два типа цельнопластиковых лопастей рулевого винта. Оба типа лопастей имеют аналогичную аэродинамическую компоновку и лонжерон с D- образным поперечным сечением. Главное их различие заключалось в том, что лонжероны лопастей первого типа изготавливались ручной выкладкой, а второго – намоткой. К серийному производству были приняты и около 20 лет производятся и успешно эксплуатируются лопасти второго типа.
Кроме лопастей рулевого винта вертолета Ми-26, примерно в тот же период времени на фирме Миля были спроектированы, изготовлены и испытаны лопасти нескольких экспериментальных винтов. Изготавливались они как методом выкладки, так и методом намотки.
Сравнение этих двух методов изготовления лонжеронов лопастей позволяет сделать вывод о том, что при использовании метода намотки создается материал, который лучше противостоит опасности возникновения складок – главного повреждающего фактора для слоистых композиционных материалов. Метод намотки позволяет также исключить из процесса изготовления лонжерона следующие операции:
– раскрой заготовок композиционного материала (при серийном производстве для выполнения этой операции необходимо специальное оборудование, стоимость которого вполне сопоставима со стоимостью намоточного станка);
– маркировку, взвешивание и селективный подбор заготовок;
– транспортировку большого числа «сырых» длинномерных заготовок препрега из зоны раскроя в зону формирования изделия (именно на этом этапе наиболее вероятно возникновение складок);
– ручную укладку и позиционирование отдельных заготовок при формировании изделия;
– ручное разглаживание и уплотнение слоев композиционного материала в процессе формирования изделия.
Кроме того, при прессовании изделий, изготавливаемых методом выкладки, возможен дрейф отдельных заготовок препрега, что в принципе исключено при изготовлении трубчатых изделий методом намотки.
Так как метод намотки позволяет изготовить потенциально более прочные конструкции, то он представляется более предпочтительным для изготовления трубчатых лонжеронов лопастей вертолета.
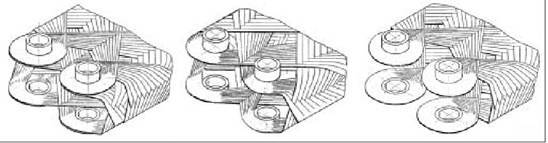
Рис. 5
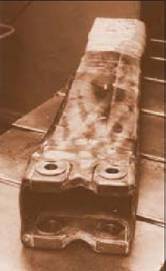
Фото 4
Одной из самых интересных работ по развитию метода намотки применительно к изготовлению композитных лопастей можно считать разработку конструкции и производственного процесса для композитной лопасти несущего винта вертолета S-76. Работы выполнялись по заказу и при техническом содействии фирмы Sikorsky Aircraft. Были изготовлены и испытаны (с весьма положительными результатами) образцы лонжеронов. К сожалению, по причинам, не имеющим отношения к технике, работы были остановлены и их результаты не могут быть представлены в данной публикации.
Для демонстрации возможностей разработанного на фирме Миля способа изготовления лопастей методом намотки в этой части статьи представлены результаты экспериментальной работы, проведенной с целью усовершенствования конструкции комлевого (присоединительного) узла композитной лопасти, и проект лопасти несущего винта вертолета Ми-60.
Комлевые узлы композитных лопастей, разработанных на фирме Миля, выполняются следующим образом. При намотке лонжеронов лопастей в комлевой части лопасти между слоями намотки укладывают дополнительные усиливающие прокладки, состоящие из слоистого композиционного материала и (или) металлической фольги. Для обеспечения необходимой адгезии поверхности фольги предварительно подвергают специальной обработке. После полимеризации лонжерона производят механическую обработку его комлевой части, сверление и расточку стыковочных отверстий так же, как это делают для металлических лопастей.
Такая конструкция присоединительного узла приводит к увеличению массы и усложняет процесс изготовления лонжерона лопасти, в связи с чем предпринимались неоднократные попытки изменить конструкцию комлевого узла лопасти и технологию его изготовления. В частности, была разработана лопасть несущего винта, содержащая трубчатый лонжерон из композиционного материала с повторяющимся перекрестным спиральным расположением армирующих волокон, которые в комлевой части лонжерона охватывают втулки стыковочного узла с изменением направления спирали.
Армирующие волокна, охватывая втулки комлевого узла, образуют слои двух различных чередующихся типов. В случае, когда угол охвата втулок армирующими волокнами меньше 180°, в процессе намотки образуются слои типа У, а в случае, когда угол охвата больше 180°, образуются слои типа Y. Слои указанных типов чередуются друг с другом, как показано на схеме (рис. 5).
Всего было изготовлено и испытано около десяти образцов лонжерона с комлевым узлом описанного типа. Вид одного из образцов до испытаний и характер типового разрушения образцов показаны на фотографиях (фото 4, 5).
Ни на одном из образцов во время испытаний не было отмечено разрушений по проушинам комлевого узла. В разработанной конструкции за счет прямой передачи нагрузок с армирующих волокон на втулки удалось обеспечить необходимую прочность комлевого узла при значительно меньшей массе. Кроме того, удалось снизить трудоемкость изготовления лонжерона и повысить коэффициент использования композиционного материала.
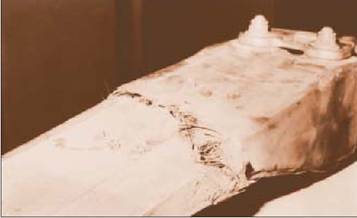
Фото 5
