Вот разметчик с помощью крана уложил на стол большой стальной лист. Затем он смотрит в лежащий перед ним эскиз и, действуя метром и циркулем, уверенно переносит на лист линии контура детали или, наложив шаблон, просто обводит его острой стальной чертилкой. Подручный разметчика легкими ударами молотка по заостренному внизу стержню — керну — делает эти линии отчетливыми и надолго сохраняющимися. Каждая деталь, намеченная такими точечными линиями, идет дальше на участок обработки.
Плаз — дорогостоящее сооружение. Кроме того, на плазовой разбивке корпуса и разметке деталей долгое время занято много разметчиков высокой квалификации. Все это заставило судостроителей искать новый, более совершенный способ раскроя деталей корпуса. И они нашли такой способ. Он называется фотооптической разметкой деталей.
Хотите узнать, что это такое?
Представьте себе проекционный фонарь, лучи которого направлены на подготовленный к разметке стальной лист.
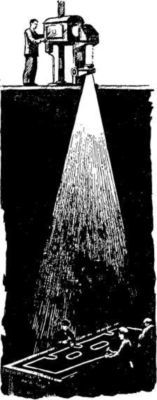
Этот способ называется фотооптической разметкой.
В фонарь вставляют негатив снимка чертежа детали. И на листе с нужным увеличением отчетливо проектируются световые линии раскроя детали. Остается навести их устойчивой краской или набить по ним керном точки. А такую работу может выполнить и малоопытный рабочий. Не нужно и плаза. Негативы снимков дает специальное бюро. Конструкторы этого бюро прямо по теоретическому и рабочим чертежам изготовляют чертежи-шаблоны каждой детали в уменьшенном виде. Затем их фотографируют. Такой способ гораздо дешевле и ускоряет разметку деталей почти в три раза.
Материал для костюма после раскройки разрезают. То же самое делают и с раскроенными листами стали, идущей на постройку корпуса. Прежде для этого применяли пресс-ножницы. Они резали сталь и долго и неточно. Теперь режут газом. Чаще всего — газорезательными автоматами. Самая интересная часть такого автомата — магнитная головка с роликом. Движение ролика передается другой важной части — копирующему устройству. Это устройство перемещает резак так, что он вырезает детали самой сложной формы без всякой предварительной разметки на стальном листе. Надо только иметь набор копир-щитов. А копир-щит — это фанерный или тонкий металлический лист, к которому прикреплены стальные прутки — копиры. Расположение этих прутков как раз соответствует контурам деталей. К копирам и прижимается ролик магнитной головки. Такое устройство заставляет газовый резак, а то и несколько резаков сразу, совершать свое удивительное путешествие, в точности повторяя движение магнитной головки вдоль причудливых границ копиров. Из резака вырывается узкая струя синеватого пламени, оставляя позади себя в металле тонкий и чистый разрез.

Так устроен газорезательный автомат. 1 — прутки на копир-шаблоне; 2 — магнитная головка; 3 — газовый резак; 4 — стальной лист; 5 — вырезанные детали.
Сейчас придумали еще более удивительную машину. Около нее уже нет громоздких копир-щитов. Но резак по-прежнему, без помощи человека, вырезает детали различных очертаний.
Кто же управляет его движениями? Может быть, человек-невидимка? Ничего подобного! Чтобы выяснить это, пройдем в небольшое помещение, неподалеку от чудо-машины. Здесь на столе установлен какой-то прибор, напоминающий радиоприемник. Но, в отличие от радиоприемника, к этому прибору пристроен объектив, почти такой же, как у фотоаппарата. Объектив «смотрит» в лежащий перед ним чертеж вырезаемой детали и с помощью фотоэлектрической копировальной системы заставляет резак издали копировать линии этого чертежа на стальном листе, да еще в нужном масштабе. Точность работы такой машины прямо чудесна. Появление ее является заслугой советских ученых. Но замечательно и то, что ее может обслуживать только рабочий со средним образованием. Таких умных машин и таких рабочих уже немало в цехах судостроительного завода.
Однако не каждая вырезанная из стали заготовка есть уже готовая деталь. Ее иногда нужно согнуть по форме корпуса парохода. Простую погибь делают на гибочных вальцах. А для гибки ребер корпуса есть специальные станки. Все это довольно легкие и быстрые операции. Другое дело, когда листу надо дать сложную погибь — и вдоль и по ширине. Раньше такую гибку делали только вручную. Сначала нагревали листы до белого каления, а потом выколачивали тяжелыми молотами по особым каркасам. Это была очень тяжелая и долгая работа. Для ее выполнения требовалась целая бригада самых опытных и сильных гибщиков. Теперь же листы гнут в холодном виде на гидравлических прессах. Такой пресс стоит недалеко от газорезательной машины. Высотой он с двухэтажный дом. На его пульте управления множество всяких ручек и приборов. В передней части пресса движется вверх и вниз большой поршень. Его называют пуансоном. Пуансон с большой силой давит через специальные штампы на стальной лист. Несколько нажимов пуансона — и лист приобретает любую сложную форму погиби. Сила давления у некоторых прессов достигает 2000 тонн.
Обработанные детали проверяет контролер, после чего их сдают на склад. Со склада они, по мере надобности, отправляются в сборочно-сварочный цех. Там из них собирают конструкции корпуса парохода. Как видите, судостроительная сталь, прежде чем сделаться готовой деталью, проходит три — четыре операции. А всего лет пятнадцать назад такому же куску стали надо было пройти десять — двенадцать операций. Корпусообрабатывающий цех завода был до отказа заполнен различными станками и прессами. Почти все они существовали для того, чтобы обслуживать клепку. Тут были дыропробивные прессы и станки для сверления в деталях отверстий под заклепки. Тут были строгальные станки для строжки кромок листов после грубого реза на пресс-ножницах. Были и станки, отгибающие фланцы (бортики) у концов листов, опять-таки для плотности заклепочных соединений. Было много и других грохочущих, громоздких станков. Теперь большинство из них исчезло.
Что же случилось в судостроении? Что могло ликвидировать множество станков, сократить число операций обработки судостроительной стали и этим самым ускорить постройку пароходов? Причиной этого явилась электросварка металлов, заменившая собой клепку.
Дуга-чудесница
Конечно, разговор пойдет не о той дуге, которая нужна, чтобы запрячь лошадь. Наша дуга совсем маленькая — длиною не более 3–4 миллиметров. И служит она для соединения отдельных частей металлических конструкций. Эту дугу можно увидеть повсюду: в усадьбах машинно-тракторных станций, при прокладке газопроводов, на строительстве мостов и пароходов. Что же это за дуга? Давайте понаблюдаем за действиями рабочего, создающего такую дугу. Только наденем очки с темными стеклами, чтоб не испортить глаза. Вот рабочий поудобнее устроился у пригнанных друг к другу деталей. Вот он тоже прикрыл глаза щитком с темными стеклами, а правой рукой сжал ручку со вставленным в нее электродом. А к электроду тянется, как змея, толстый серый провод от источника тока. Свариваемая конструкция заземлена. Тут получается как бы электрическая цепь. Пока электрод не касается изделия, цепь разомкнута, ток выключен. Вот сварщик чиркает электродом по металлу, как спичкой о коробку, и слегка отводит электрод от металла. Сверкнули искры, а потом между электродом и металлом вспыхнула ослепительная дуга. Направляемая рукой рабочего, она медленно поползла вдоль стыка деталей. Ее пламя невыносимо для человеческих глаз. И это неудивительно: температура дуги достигает 3500°. Это только в полтора раза меньше температуры раскаленного солнца. От такой температуры кромки деталей и электрод быстро расплавляются и детали свариваются.
Вот рабочий отвел кончик электрода от металла на расстояние больше, чем 3–4 миллиметра. Электрическая цепь размыкается — и дуга гаснет. Теперь можно беспрепятственно любоваться чудесной работой нашей дуги. Она образовала на стыке деталей блестящую чешуеобразную дорожку — шов. Шов накрепко соединил в одно целое обе детали. Такой способ соединения называют дуговой электросваркой.